The SDGs provide an opportunity for companies to create value for both their business and society.
We have considered how our business operations contribute to achieving the 17 goals of the SDGs.
There are a variety of ways to work toward the goals.
We fully utilize our strength of each site to address social issues from multiple angles as well as ensure our steady growth.
France
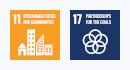
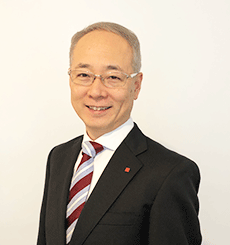
Responsible Sourcing
Motonobu Sekine
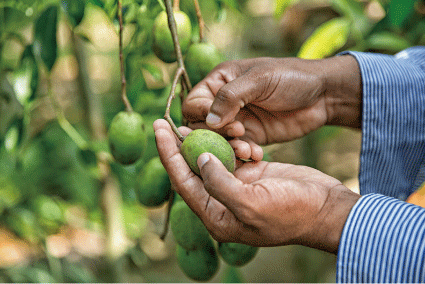
The COVID-19 pandemic has brought out the reality in an unexpected way: the world is facing global environmental emergencies such as climate change and biodiversity loss that threaten to wreak economic and social havoc. As such, it is now essential to review our supply chain to make it more transparent, resilient and inclusive, thus creating long-term value for the company and all its stakeholders.
In light to this situation, a more responsible sourcing strategy has been materialized through the “Responsible Sourcing Policy”. TEPL actively participates in the deployment of these commitments and strategy and works for the preservation of the resources and the well-being of the society, by associating itself with new partners throughout the world.
This is notably the case in Sri Lanka, where we have made a commitment to a young supplier. We quickly transformed it into a business success story.
Thanks to this partnership and to the income it generates, we ensure their families a stable salary, access to education and the preservation of their environment. Moreover, our proximity to this supplier allows us to identify the current and future needs of their families and offers us the possibility to support them in their daily life.
By producing fragrances from more responsible sources, we participate in the creation of a more virtuous circle where all the actors will be able to take advantage of this partnership and answer the ecological and social matters.

PROFESSIONAL GENDER EQUALITY INDICATOR F/M
95/100
Pay gap between men and women : 35 points out of 40
Difference in the distribution of individual salary increases and promotions between men and women : 35 points out of 35
Percentage of female employees who got salary increases when returning from maternity leave : 15 points out of 15
Parity among the 10 highest salaries : 10 points out of 10
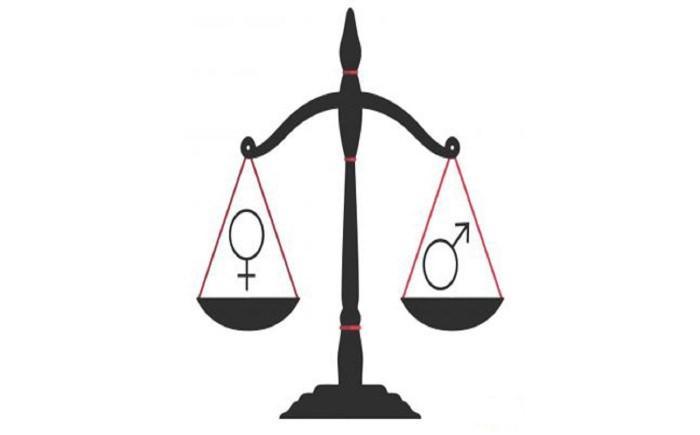
Singapore
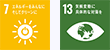
USA

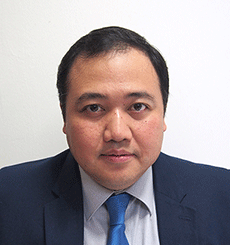
Solar Power Generation, Clean Renewable Energy
Andy Arguelles
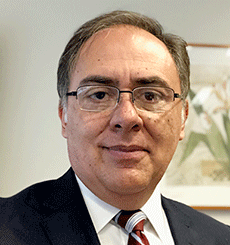
Gender Equality
Luis Pinedo
Solar energy is the most viable clean renewable energy source for Singapore as Singapore receives an average of 5.5 hours of sunshine a day, or an average annual solar irradiance of 1,600kWh/m2. Solar PV (Photovoltaic) system generates less CO2 emissions than fossil fuels, contributing to environmental sustainability.
As part of Takasago Singapore’s (TIS) commitment to environmental sustainability, TIS has partnered with Sunseap, a local clean energy solutions company, for the installation of solar PV panels on the rooftops of the factory and administrative building at Sunview Road when we relocated from the old production site in fiscal 2014. We have signed a 20-year solar power purchase agreement (PPA) with Sunseap where Sunseap installed the solar geneartion system without requiring any upfront investment cost for TIS. TIS is only charged for the solar energy consumed monthly at a competitive electricity tariff rate. The solar geneartion system started power generation in fiscal 2015 and supplied about 3% of the annual electricity consumption at TIS.
To continue this initiative, TIS management decided to proceed with second phase of solar generation system and installed additional solar PV panels over the air-conditioning condensers on both buildings in fiscal 2017. The total generating capacity of the solar PV panels installed at TIS is now 275kW and supplies about 3.3% of the annual electricity consumption at TIS (10% increase compared to Phase 1), thereby reducing carbon footprint at TIS by 122 tCO2/annum.
TIS has engaged Sunseap for annual cleaning of panels’ surfaces and maintenance service of the solar generation system to ensure that the solar PV panels are in good working conditions and generating electricity efficiently.
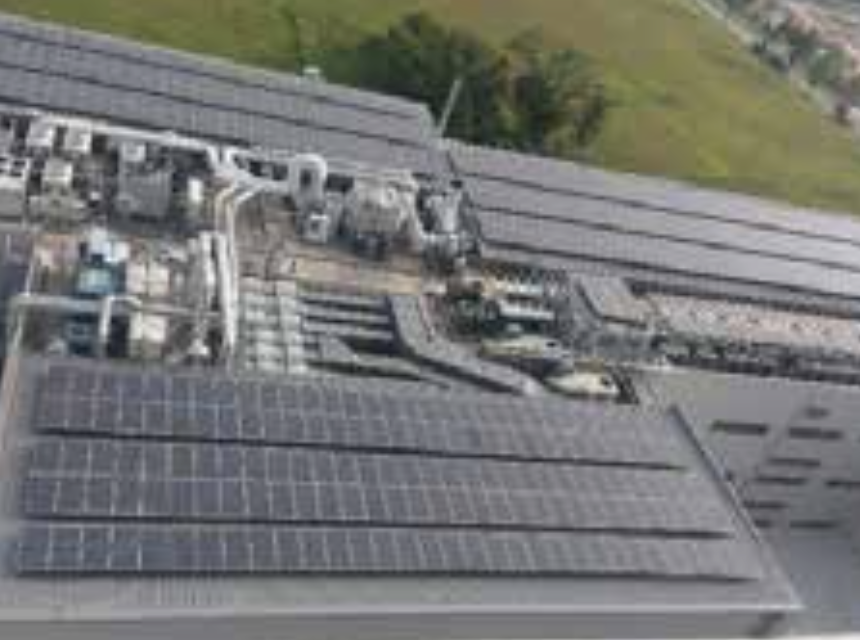
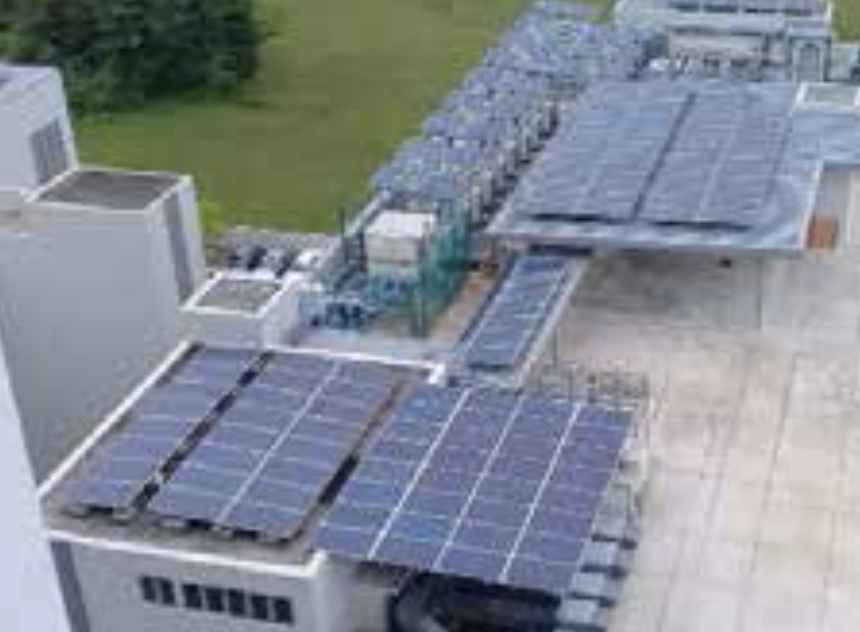
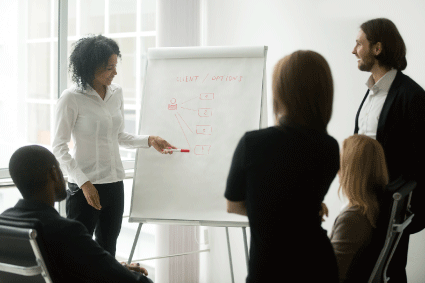
Although the situation is improving, women continue to be impeded in the compensation area because they are often required to take time off from work to be the primary care-giver of their children as well as manage other family obligations. The break in service has a negative effect on a steady work history, which in turn, results in the discrepancy in pay, for similar jobs. It is estimated that women who left the workforce due to caregiving responsibilities and return to work will receive an offer that is 7-10 percent less than an employee who is currently working, perpetuating the pay disparity.
In recognition of this long-standing pay differential, Takasago USA, consistently and regularly reviews the compensation rates for employees to ensure there is equitable pay.
Specifically, regular compensation and pay equity audits are conducted to analyze the compensation rates by gender to determine if there are any gaps or areas of concern in what the female employees are earning compared to their male counterparts. If imbalances are found, immediate steps are taken to remedy the situation and make appropriate adjustments. In addition to performing regular pay audits to root out inequities, regular salary analysis are conducted regarding compensation in the Fragrance and Flavor industry to ensure our rates remain competitive.
Another initiative taken at Takasago USA to eliminate disparity between pay is to cease requiring salary history information during the recruitment process.
As outlined earlier, women have historically earned less than men for the same or similar positions.
Using past salary information to gauge offers of employment serves to perpetuate this pay disparity.
Instead, Takasago sets fair and equitable market rates for positions and candid discussions are provided with candidates on those pay ranges.
Job offers and employee salary adjustments are based on the position, skill, experience, and merit of the individual, not on the personal or historical compensation.
Another area that has been an historical obstacle to achieve gender equality affecting mostly, although not exclusively, to women in the workplace is harassment. While the “#MeToo” movement has brought more focus onto the problem, mistreatment remains and can be a hinderance to gender equality.
Takasago does not tolerate any type of discrimination. In an effort to educate and train employees, mandatory training is provided to all employees on anti-harassment and acceptable workplace behaviours. The training includes obvious as well as subtle ways harassment can
occur. Managers, in particular, are also trained to understand the impact of gender biason decisionmaking and personnel actions. Performance
evaluations are carefully reviewed to ensure managers have not systematically rated higher based on gender and clear and consistent criteria is applied to make personnel decisions unbiased.
Spain

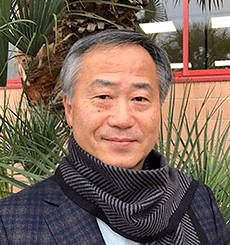
Promotion of Health Habits at Work
Hiroyuki Matsuda
The epidemiological report elaborated after the annual medical checkup of Takasago Spain (TICSA), employees showed general information about some health aspects such as mean body mass index, overweight, smoking habit, sleeping habit, etc. With the goal to improve health indicators and quality of life of our employees, TICSA has prepared number of training activities. TICSA strives to improve the health habits and the wellness of the employees through education and training courses and follow the physical index through the years.
The Training Week 2021 was held during the 7th, 8th and 9th of April at TICSA, coincided with the World Health Day, as the first course of Health Habits.
In this activity, attended by most of our employees, it was treated the need to create healthy lifestyle habits that allow a full healthy life and prevent health problems. It was taught to assess the negative repercussions of certain behaviors on health and quality of life and the benefits of physical exercise habits, hygiene, balanced diet, and everything that in general contributes to leading a healthy life.
This training aims to be a chance for the employees to change their lifestyle to be more healthy and improve their quality of life. The company will continue working toward this goal and hold activities and workshops to encourage employees to set their own health related goals, taking account advices from experts in the field.
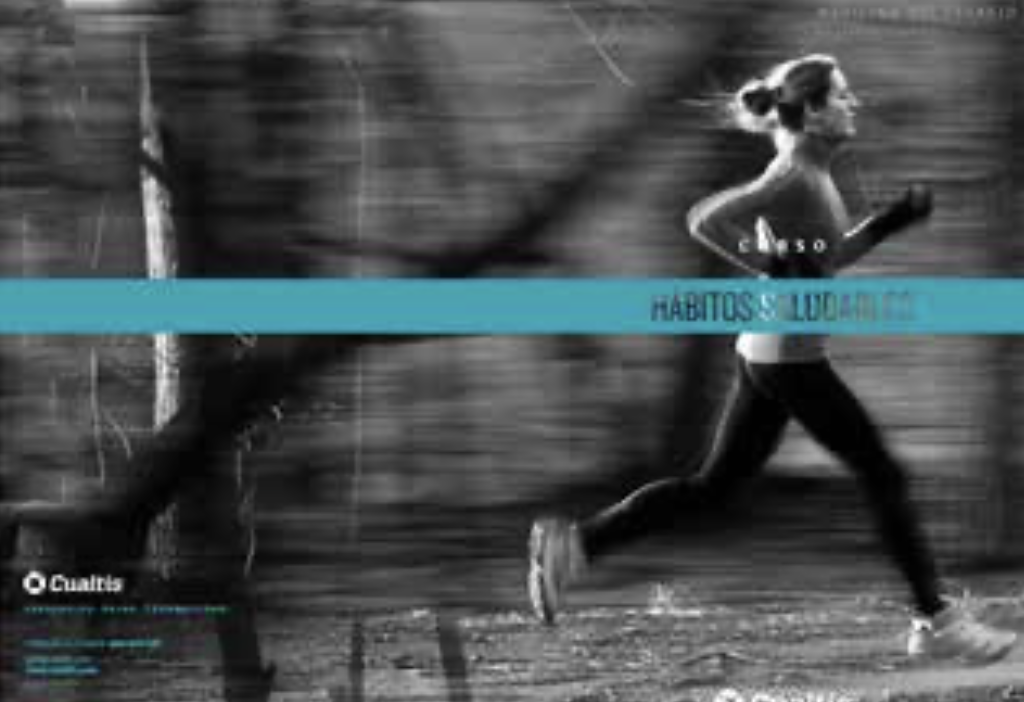
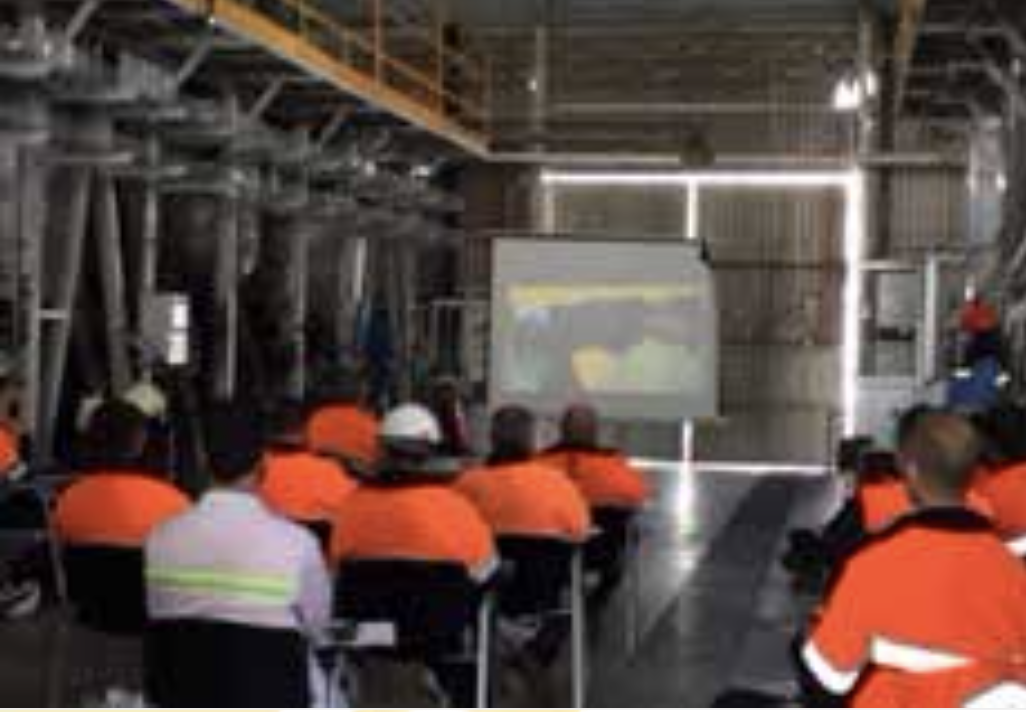
Germany
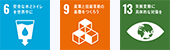
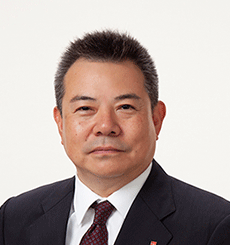
Vapor Heat Recovery
Akihiko Kawano
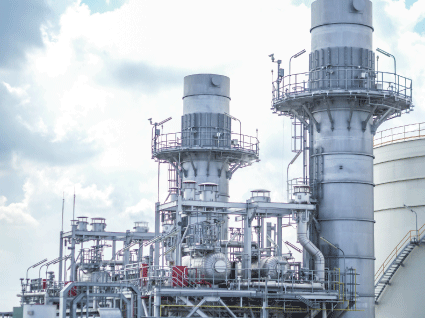
We extend the factory’s heating network at the Zülpich site to integrate as much diffuse heat sources as possible into this system. By using these heat sources, stress on the heating system can be relieved and the primary energy demand for heating can be reduced. Condensate collection tanks in the plant’s steam network are an essential heat source. Steam condensates are collected and returned to the boiler house via pumps. These collection tanks are atmospherically ventilated and considerable amounts of steam are produced during expansion. These vapours are lost through the roof. This residual steam is to be used energetically. As a result, more condensate can be recovered, the heating system is relieved and less steam is needed to degas the already hot feedwater in the boiler house.
By relieving the reverse osmosis system, less fresh water is needed and the amount of waste water is reduced.
Since the heating system is nearing its limit due to the continuous expansion of the plant, these measures can postpone major replacement investments or even make them unneccessary.
A condensate collection unit was selected for initial trial. After analyzing the flow volume, a suitable location for shell-and-tube heat exchanger was calculated and installed accordingly. In order to record the savings, a suitable measuring system was also installed. During planning, an ROI of 8 months was forecasted.
After the delivery of the components, the system was installed and commissioned in three weeks.
The forecast of the planning could be fully confirmed by the measurement. An identical system will also be installed in TEG’s new naturals area and additionally we plan to install a system directly in the boiler house. Here, the vapours from the degassing of the steam plant will also be fed into the heating network.
Shanghai
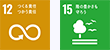
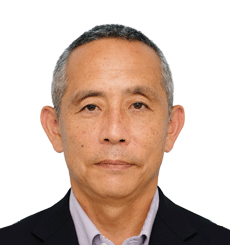
Developing Environment-friendly Flavors
Sumio Sakai
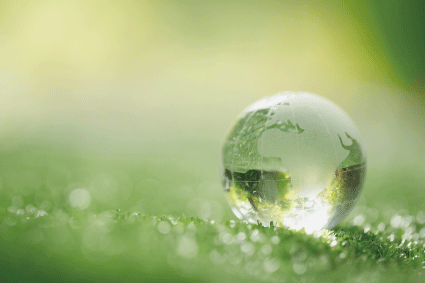
In accordance with Takasago’s strategy, we are proactively using l-Menthol, one of the main raw materials produced from bio-based materials, to promote the development of flavors for oral care and confectionery. This enables us to propose flavors with a lower environmental impact that incorporate “green chemistry,” which uses renewable raw materials, into the formulation of raw materials as well.
In terms of natural raw materials such as citrus oil, we are promoting the effective use of natural resources by consolidating oil raw materials used locally and also by studying harmonization on a global scale.
In addition, in order to resolve concerns about the supply of citrus oil as a raw material in the future, we are studying the possibility of introducing chemicalbased oil alternatives into some of our formulations to reduce the amount of natural oil used. This will further promote the effective use of natural resources and contribute to the development of flavors with more stable quality.
Guangzhou
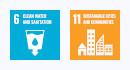
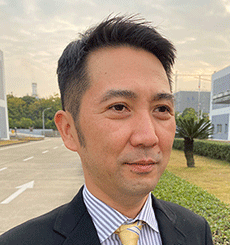
Water Resources Protection
Yuichi Tobe
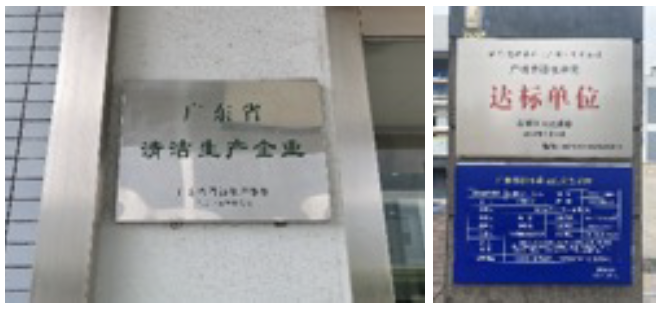
Right: Plaque of Up-to-Standard Drainage Company
Water resources protection is an indispensable part of environment protection and one of the priorities of TIG throughout its business process, which is in line with the Sustainable Development Goals related to clean water and sanitation.
In terms of water saving, TIG has been collecting condensate generated from steam in workshops and reusing them for heating boilers for many years, which helps to improve the cyclic utilization rate of water. In addition, TIG places importance on clean production and has been awarded with the title of Excellent Enterprise on Clean Production of Guangdong Province in China. On this basis, TIG continues to promote clean production and take various measures, such as introducing new spray headers with higher efficiency for CIP in the new factory to save water and replacing the RO water machines to improve the water production rate.
Regarding prevention of water pollution, TIG conducts diversion of stormwater and wastewater and carries out sampling test of stormwater twice a year for effective monitoring. In addition, TIG has changed all closed pipelines and conduits designed many years ago into exposed ones so that they ares more convenient for the staff to observe any unusal situation or potential leakage and prevent pollution. Furthermore, TIG is one of the companies that have obtained the Plaque of Up-to-Standard Drainage Company at the earliest time according to the latest requirement of local authority.
TIG aspires to fulfill its corporate responsibility and contribute to society through business activities. TIG will spare no efforts to pursue sustainable development together with the Takasago Group.
Brazil
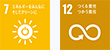
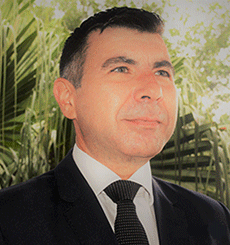
Energy Consumption is 100% from Renewable Sources!
Adilson Azevedo
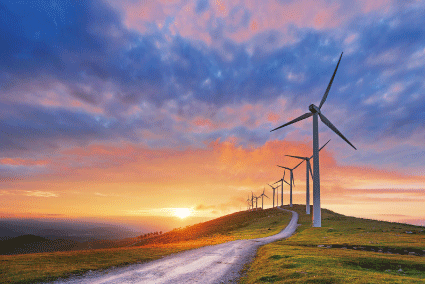
In July 2020, Takasago Brazil (TBR) migrated from the Captive Energy Market to the Free Energy Market (competitive environment for negotiating the value of electric energy). The energy used comes from small hydroelectric plants, biomass, wind and solar power, which have the characteristic of generating clean energy.
The free energy market allows consumers to buy energy directly from generators or traders by negotiating deadlines, price and volume, and only the physical supply of energy is continued with the distribution concessionaire. The regulated tariff is only for the distribution service and energy becomes fixed value, while the payment involves the distribution and generation of energy in the captive energy market, based on tariffs regulated by the Government.
The migration to the Free Energy Market enabled TBR to reach the global goal of using 100% renewable energy, in addition to contributing to the reduction of CO2 emissions and fostering the production of clean energy.
In addition, it has led to other benefits, such as: more flexibility (free choice of energy supplier and upstream of consumption), less costs
(direct negotiation of the price of energy), more savings (discount in the distribution tariff), more profitability (enabling the “sales” of residual energy) and more certainty, avoiding envrironmental impact
with the variation of regulated tariffs.
Mexico
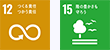
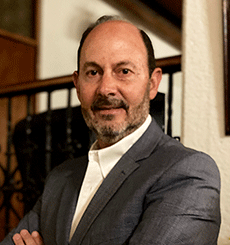
Zero Waste to Landfill
Humberto Campos
In June 2020, Takasago de México (TDM) developed and implemented the “Zero Waste to Landfill” initiative, this is based on the premise that the waste produced in the industrial field is recoverable and reusable if treated properly, transforming waste into valuable resources.
The “Zero Waste to Landfill” initiative has a single goal: to divert 100 percent of industrial waste to local landfills for reuse, recycling, composting and incineration of waste for power generation. To achieve this objective, TDM made a strategic alliance with GSCP Servicios Sustentables.
At TDM the packaging materials such as metal and plastic drums of different capacities are reused in other processes; scrap metal, low-density plastic, paper and cardboard are sent to recycling; organic waste such as powder of the process, food and garden waste are processed to become soil improvers and finally those wastes that cannot be recycled, reused or remanufactured are used for power generation.
This initiative has enabled TDM to indirectly reduce water and energy consumption and CO2 emissions by avoiding the manufacture of raw materials right from the start as well as conservation of natural resources that would have been required for their manufacture.
Other benefits include: lower materials disposal costs, additional income from the sale of industry by-products and improved relationship with local governments.
With the “Zero Waste to Landfill” initiative, TDM favors the optimization in the use of energy, raw materials and natural resources, contributing to the circular economy and sustainability.
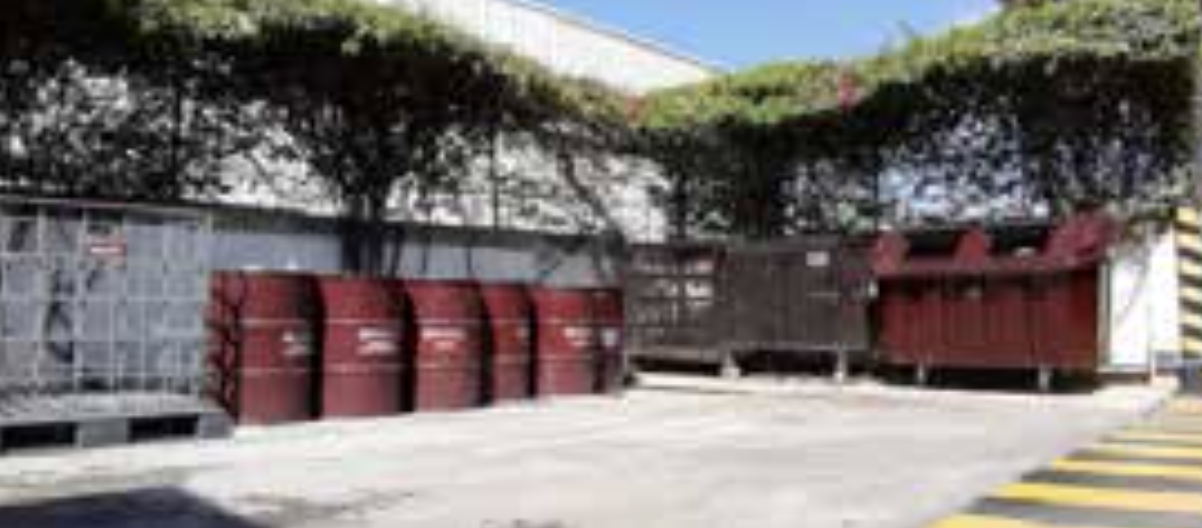
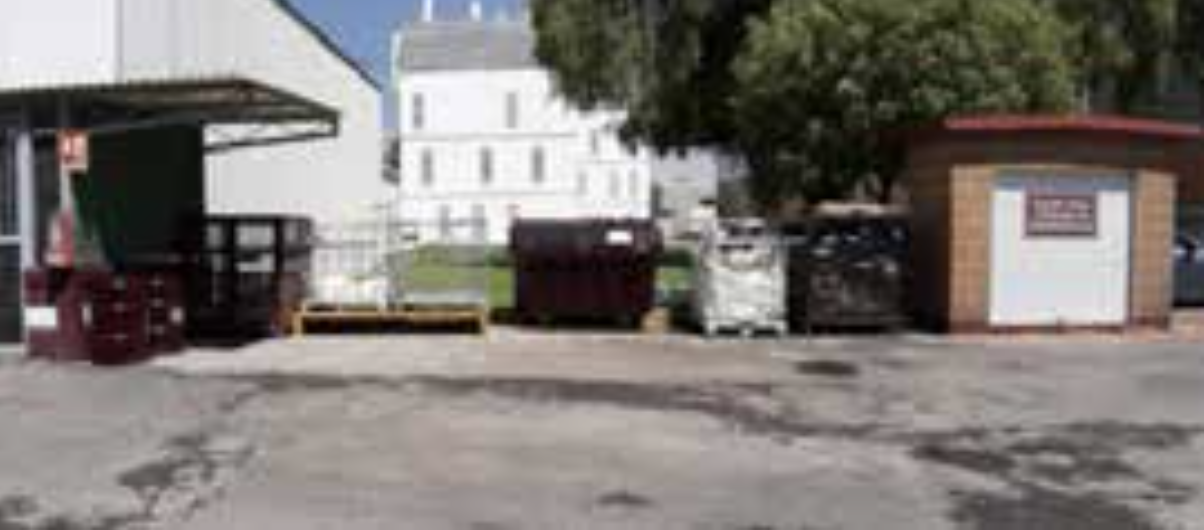